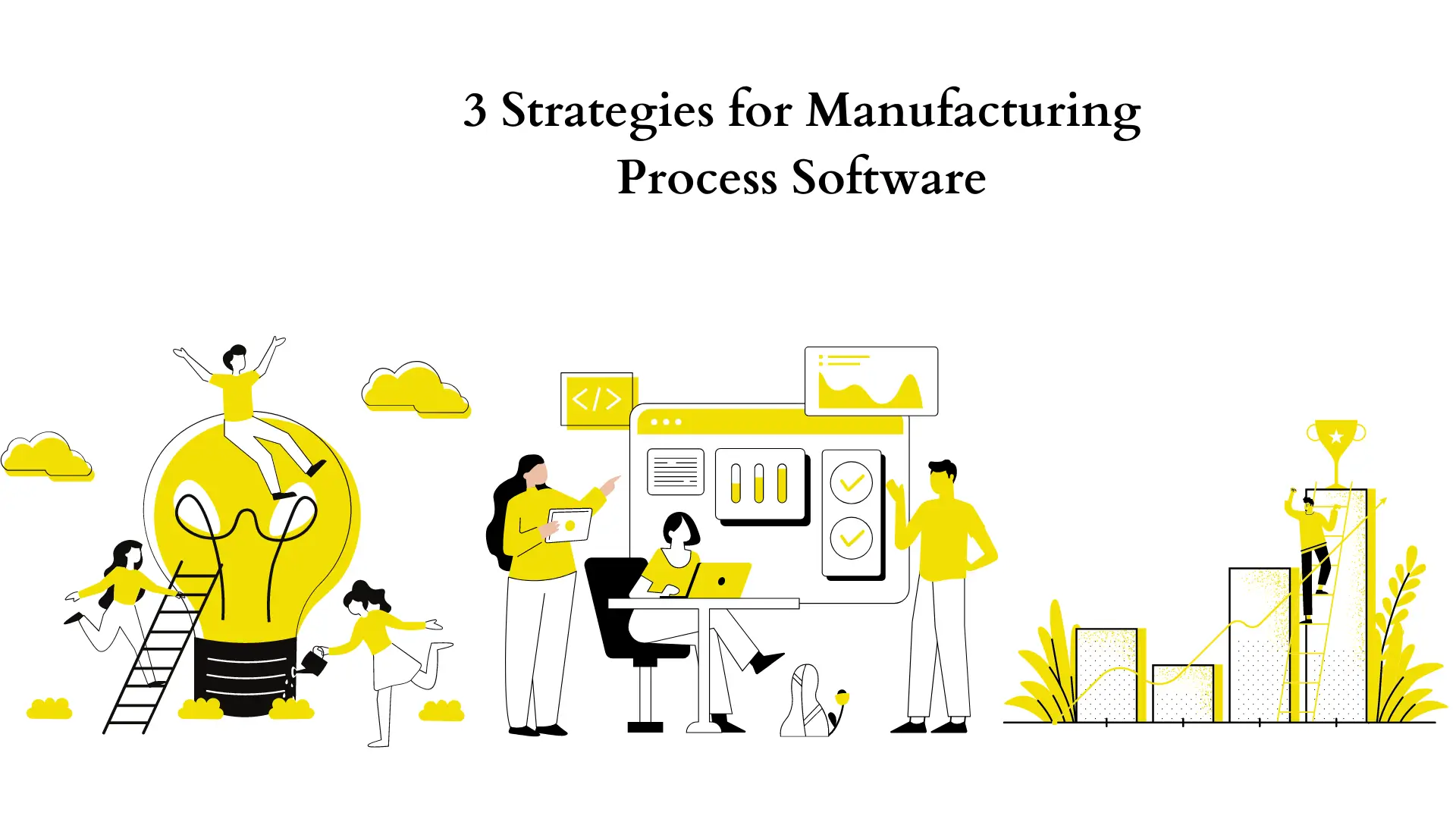
Industrial software has emerged as one of the most dependable automation solutions for various manufacturing firms worldwide. The need for automated systems has risen considerably with the advent of Industry 4.0, the fourth industrial revolution. Building on the business backbone, often ERP, may make sense for some organizations looking to expand their manufacturing operations capabilities.
Building on current manufacturing operations management (MOM) or industrial automation investments makes sense for others. Manufacturing software may dramatically boost productivity and operational efficiency.
We’ve identified three potential ways: a top-down or ERP-centric strategy, a center-out or MOM-centric approach, or a bottom-up or industrial automation-centric approach. We’ll go through the primary benefits and drawbacks of it all.
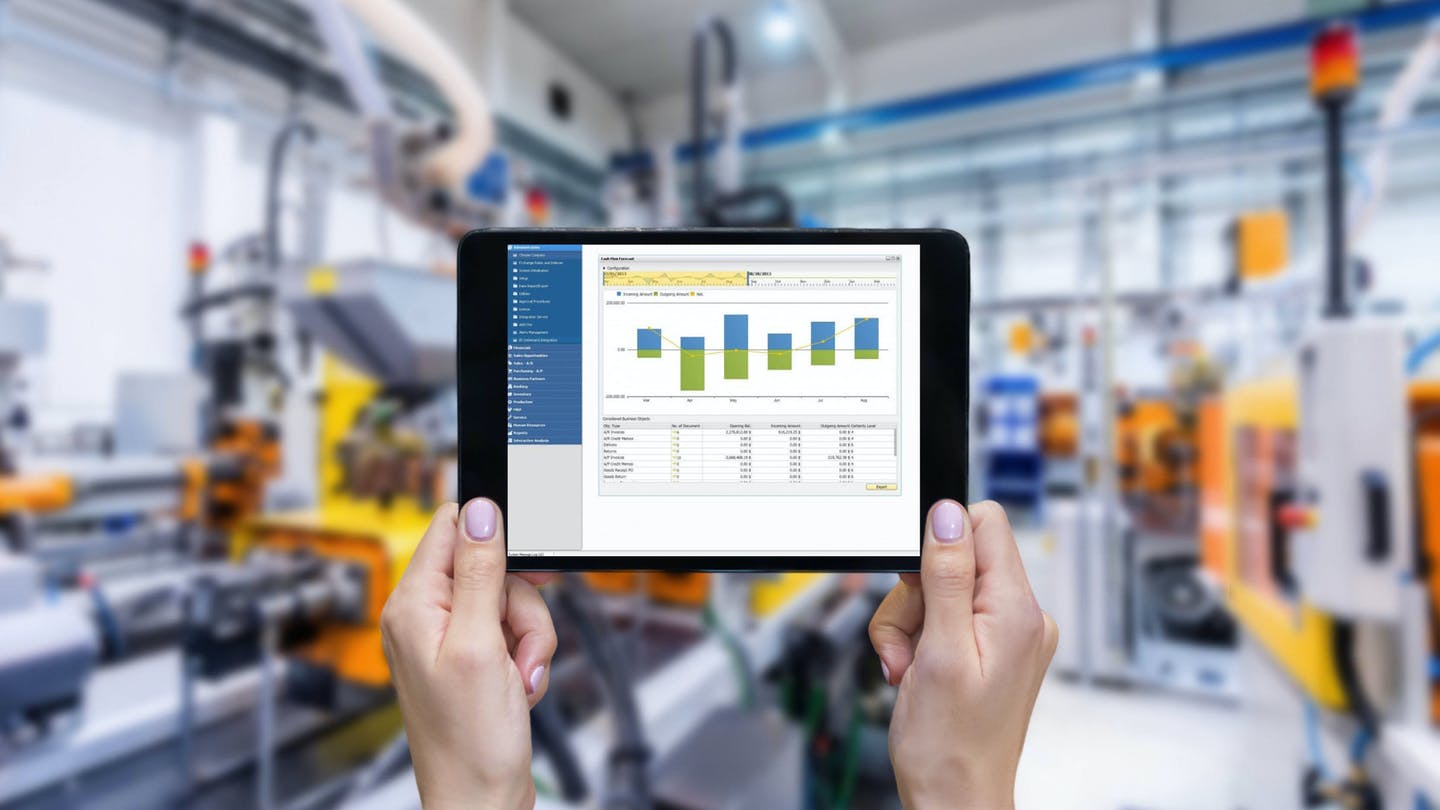
What is the purpose of manufacturing software?
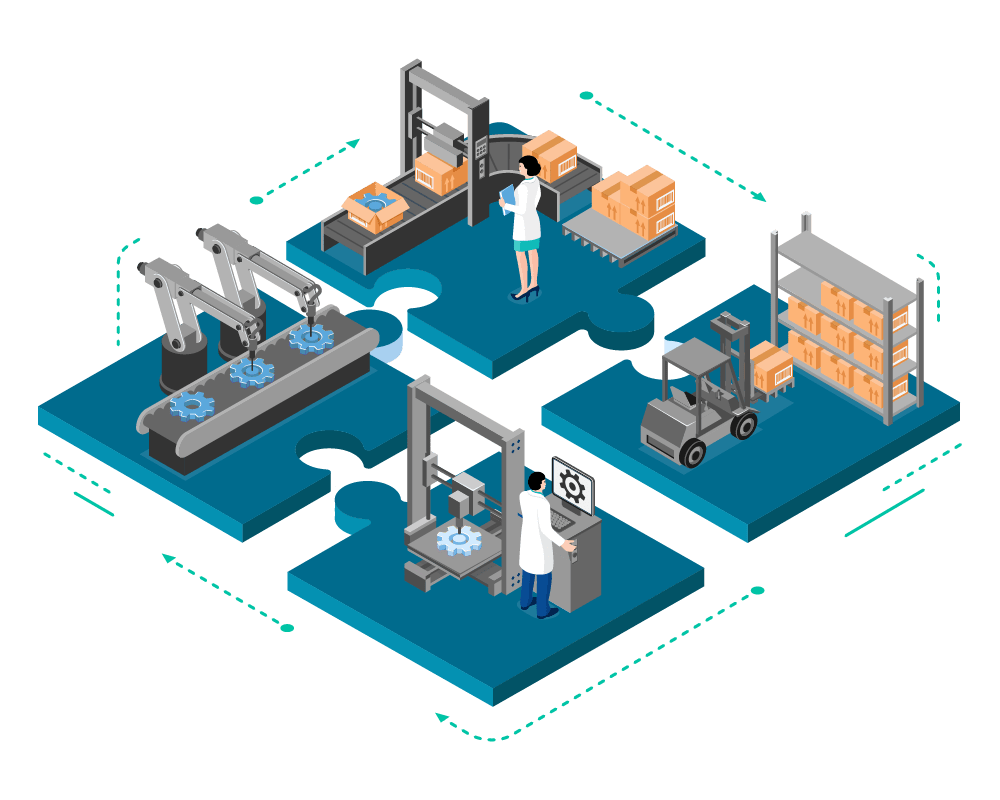
Manufacturing software automates production procedures on the shop floor, from production planning through stock availability tracking, resource allocation, job delegation, and production routing.
Understanding the Different Manufacturing Software Strategies
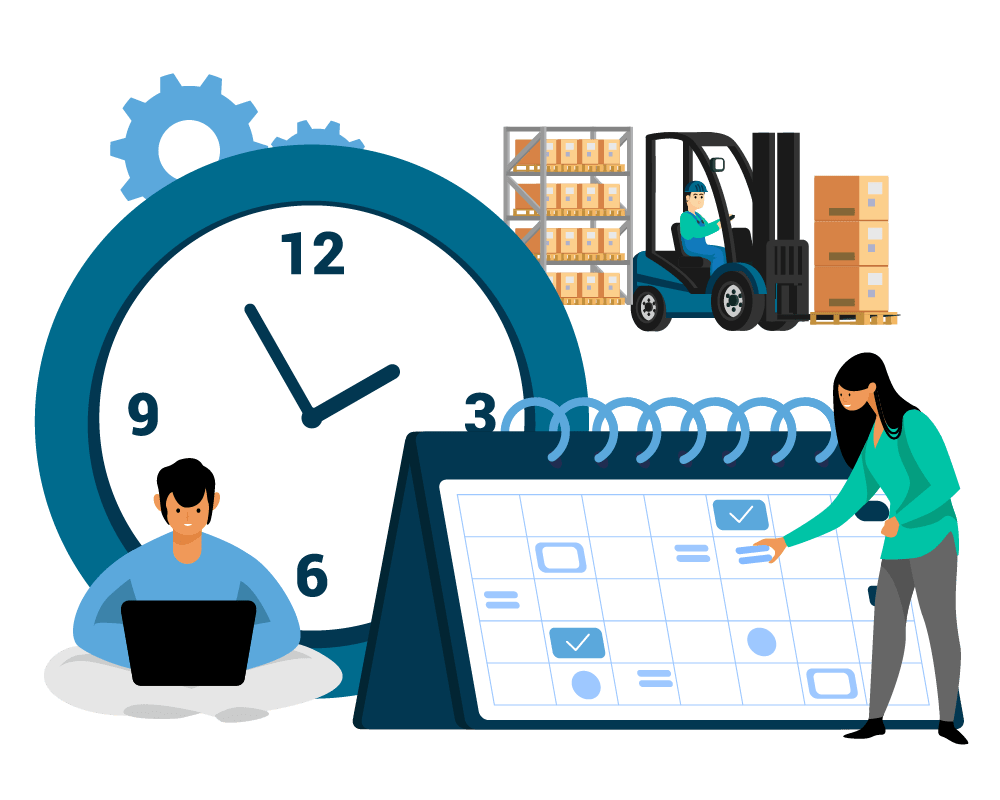
While it’s common to simplify and consolidate processes where possible, it’s also critical to integrate key processes and ensure that the systems that support manufacturing operations improve the business rather than simply feeding information to other systems and people in the organization. This is a tactical strategy, and the approach may change based on your previous investments.
Top-Down/ERP-Centric Manufacturing Strategy
A top-down software strategy leverages the existing ERP framework as a foundation for further development.
Pros: One of the most significant benefits of this method is the ability to have tight integration/enforcement between business and production processes and master data consistency.
Furthermore, ERP-centric manufacturing IT structure integrates business and manufacturing knowledge and fewer IT vendors and control points for enterprise application integration.
However, you will still need to input real-time information via connecting to the automation layer for many industry use cases.
Cons: An ERP-centric strategy has several drawbacks, one of which is its lack of adaptability. Any modifications in production processes or upgrades are more difficult to execute due to the inherent rigidity of an ERP system.
These usual procedures need to be changed much more quickly than business processes. Furthermore, the manufacturing functionality is not always as comprehensive as a manufacturing-specific (center-out) strategy, leading to performance and availability difficulties.
This category includes SAP, Plex Systems, Oracle, and Epicor. Nevertheless, a wide range of vendors serves this market.
Center-Out/MOM Software-Centric Manufacturing Strategy
Pros: The manufacturing operations management (MOM) software tools that support plant operations are the foundation of a center-out or MOM-based IT model. One important advantage of this technology is the wide range of manufacturing capabilities. It interfaces seamlessly with corporate and automation level applications above and below, as seen in the infographic below.
This approach supports plant operations and allows for integration with various ERP, PLM, and industrial automation systems that provide detailed manufacturing intelligence capabilities, as well as typical support for enterprise application integration standards such as ISA-95 and industrial automation application integration standards such as OPC/OPC UA, which restrict and simplify integration with other systems. Unlike an ERP-based architecture, a center-out design allows more flexibility in changing production systems and processes.
Cons: One of the drawbacks of the MOM-based architecture is that it does not always scale enterprise-wide, necessitating numerous instances to manage various plants. It might not be the best solution if you have several databases to handle throughout its application set. A center-out strategy necessitates separating master data from bill of materials/ERP master data and the manual coupling of business and manufacturing operations.
Apriso, Camstar, Lighthouse Systems, Parsec Automation, Aegis Software, and iBASEt are just a few companies that operate in this field; however, there are many more.
Bottom-Up/Industrial Automation System-Centric Manufacturing Strategy
Pros: When manufacturing IT architecture is developed around an automation system, it may easily fit the automation system’s plant, area, unit, and line structure. Data is collected at a comprehensive level of operations, including what’s going on with the equipment. However, this real-time data must be modeled and connected with production data. This technique, like center-out, usually supports standards like ISA-95 and OPC/OPC UA.
Cons: A manufacturing organization often has several diverse automation systems. A bottom-up strategy does not provide a common base for standardizing applications. Because automation systems are often set from the perspective of automation processes and equipment rather than production/product manufacture, software alone is insufficient to deliver full/rich MOM capabilities.
Vendors like ABB, Emerson, AspenTech, Invensys Operations Management, GE IP, Honeywell, and Siemens, among many others, come under this group.
Which way should you go?
So, which method is the most popular and efficient? Companies nowadays typically use a center-out or top-down strategy, although diverse patterns arise based on firm size and unique vertical sector demands, and bottom-up may make perfect sense for some organizations.
The Manufacturing Operations Management Survey conducted by LNS Research delves into this and other pertinent MOM data. Find out what other major trends are emerging due to the convergence of technology breakthroughs and market demands by clicking the link below.
Manufacturing Operations Software Implementation in 5 Easy Steps
Manufacturing Operations Management (MOM) is a software category that has already demonstrated its ability to assist businesses in better manage and integrating their many business and manufacturing processes. MOM has made industrial processes safer, more efficient, and lucrative.
It’s critical to take the industry’s collective “lessons learned” from the past and apply them to future endeavors, focusing investments and teamwork on best practices.
Efforts to Improve Manufacturing Operations Management
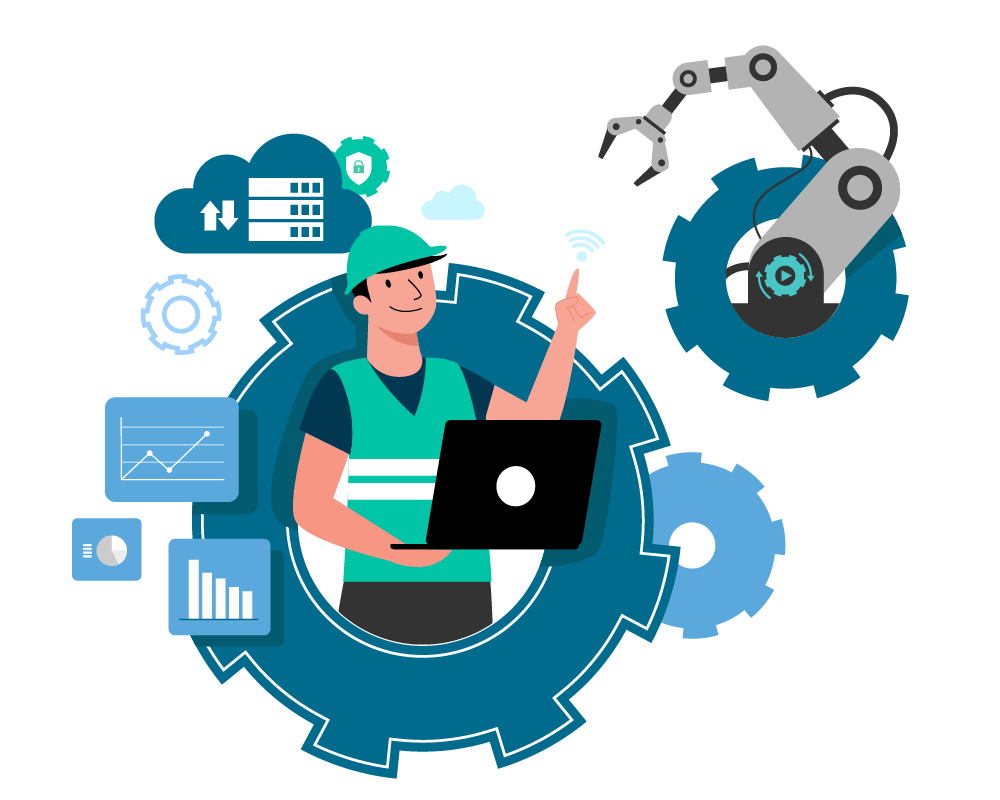
A thorough MOM implementation is difficult and can pose significant obstacles to businesses, with success reliant on aligned goals and a cross-organizational effort that considers people, processes, and technology. This article has outlined five important elements to a successful MOM deployment that will put businesses on the fast track to manufacturing operational excellence:
ENSURE EXECUTIVE DIRECTION AND LEADERSHIP
To stimulate inevitable cultural and process changes across the firm, it’s critical to have complete senior buy-in from the start. Breaking through organizational silos that directly influence industrial processes requires executive leadership. Executives must take the initiative in connecting top-level, strategic company goals to particular production plans and targets.
FORM A CROSS-FUNCTIONAL TEAM TO ANALYZE PROCESSES FROM START TO FINISH
This group should identify and understand major disconnects, such as inefficiencies, broken handoffs, information gaps, and mismatched organizational teams that do not provide “business and manufacturing” benefits through collaboration and recommendations for specific processes improvements.
Next, the team should prioritize particular activities to address these process concerns and estimate the range of business consequences and outcomes if they are resolved.
COMPILE A LIST OF ALL MOM SOFTWARE APPLICATIONS AND SUPPORTING PEOPLE THAT HAVE BEEN DEPLOYED
This applies to both in-house and packaged software. It’s also critical to identify areas where manufacturers may standardize installing manufacturing software solutions that cover a larger set of processes in an integrated manner rather than merely reproducing existing point solutions with technologically updated applications.
BEGIN WITH A MOM PILOT/PROOF-OF-CONCEPT APPLICATION AT A SINGLE PRODUCTION SITE
It’s great to practice starting with a portion of the fully envisioned capability and testing and showing that the intended outcomes are feasible. At the same time, the pilot must solve a substantial manufacturing business pain issue with a high return on investment. Completing a pilot program will enable more precise estimates of a full implementation’s time, effort, investment, scalability, and consequent business value.
USE MOM APPLICATION TEMPLATES THAT HAVE BEEN PRE-CONFIGURED
Instead of significantly modifying software to adhere to current processes, it’s typically preferable to adapt production processes to established templates given by some suppliers. These pre-configured templates frequently contain best practices, presenting a fresh chance to enhance operations. The pre-configured template technique makes the application more supportable by both the vendor and the manufacturing firm throughout a long life cycle, in addition to lowering the amount of customization necessary and speeding up time to value.
Conclusion
One of the most prominent automation technologies for enterprises is manufacturing software. This program is simple, but it is also less expensive for manufacturers. Manufacturers may mix software with the newest machinery and tools. New MOM functions become accessible as technology improves and becomes more cost-effective.
Finally, industrial software plays an important role in improving efficiency and productivity on the shop floor. On the other hand, Manufacturing ERP software is a better fit for your firm if you automate your complete business process.
Get in touch with us to know more about manufacturing process software and how it can help your business reinvent its wheels for the better.
Abhinav Sathyamurthy is a professional blogger with over six years of experience covering technical topics such as blockchain, ERP, AI, and other matters.